自家配合飼料対談(丸粒)Dialogue
![]() | ![]() |
丸粒トウモロコシ
四半世紀のチャレンジ
経営者を育んだ「自家配合」の歴史から学ぶ
丸粒自家配合対談
コーンテック社 吉角 和博 会長
林牧場 林 邦雄 会長
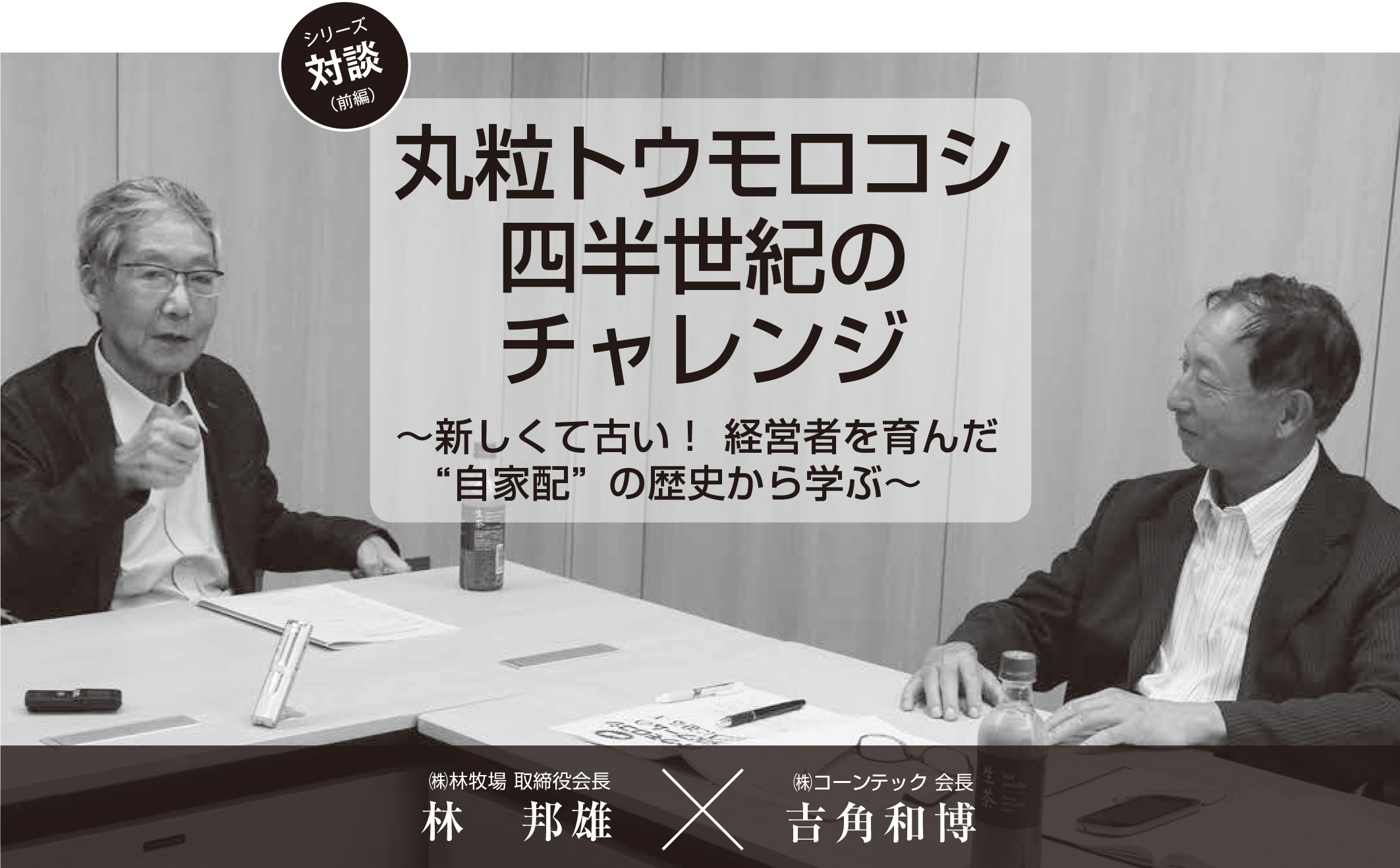
1993年(平成5年)12月にガット・ウルグアイラウンドが合意されたことを踏まえた国内対策の1つとして、それまで20年にわたって生産者団体が求めてきた飼料用丸粒トウモロコシの農家による無税輸入が解禁された。1995年4月のことであり、それから四半世紀が経過しようとしている。この間、国内最大規模の自家配に取り組んだ林邦雄氏と、自家配合施設の導入サポートで一貫して生産者と関わってきた吉角和博氏に、丸粒自家配の過去・現在・未来を語っていただいた。
丸粒第1世代は粉砕機の
更新で次のステージ
第3世代はIT・IoT化で飼養管理全体、次のステージ目指す
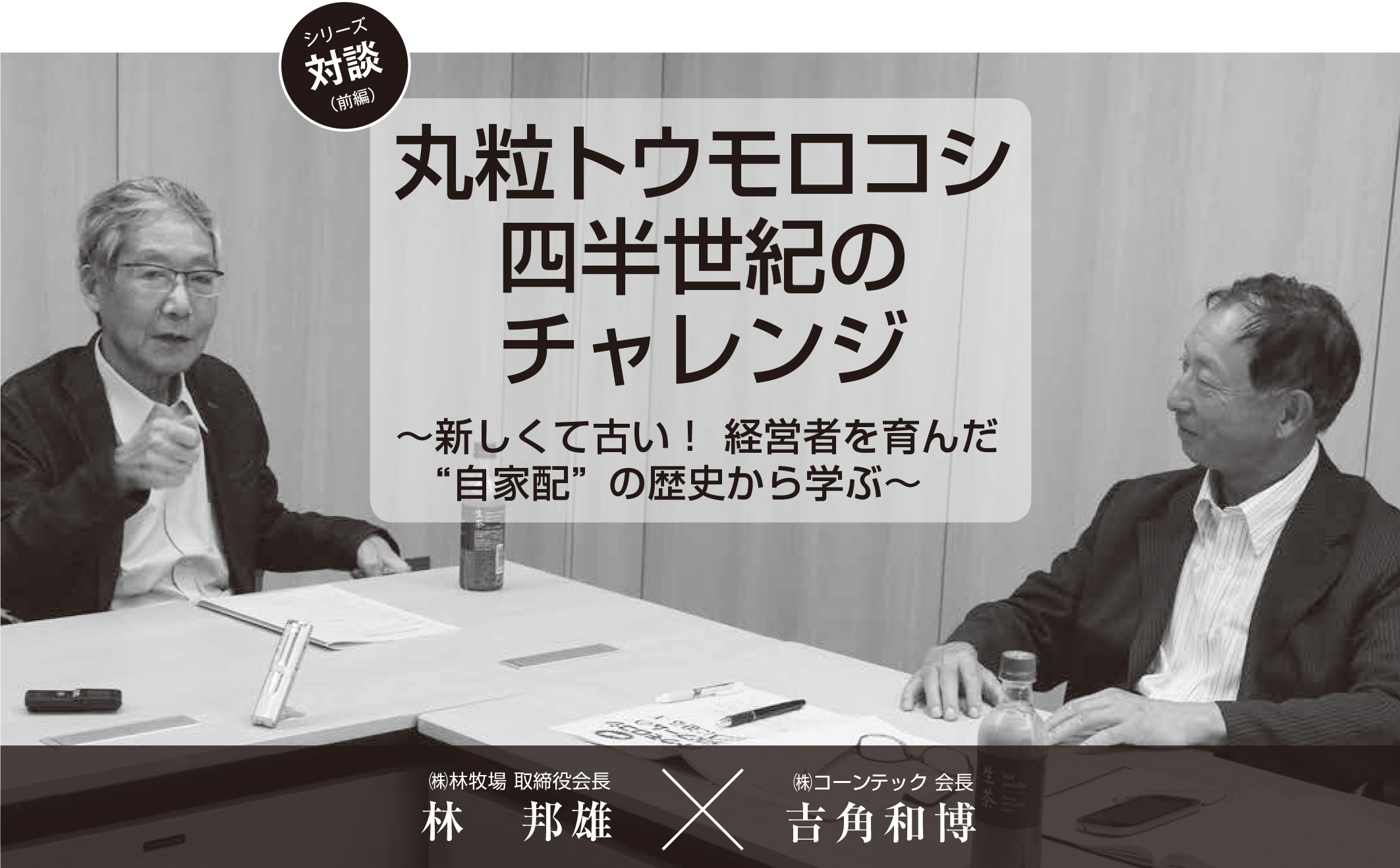
丸粒トウモロコシの無税輸入解禁に伴う自家配ブームのあと、性能の高い粉砕機の登場と、飼料用米の利活用推進という流れのなかで、新しい世代が自家配に取り組む動きが盛んになり、そこで成功した若手生産者がさらに積極的な農場展開を目指す動きを見せている。今後、人で不足がさらに深刻化していくなかで、自家配を支援する周辺業者には、単にハードとしての資材を提供するだけでなく、原料の栄養価、配合設計と現場のデータを結ぶソフト面の支援も求められている。前回に引き続き、林邦雄氏と吉角和博氏に今後の方向について議論いただくとともに、吉角氏の後継者で、IT事業でも実績のある吉角裕一朗氏に加わっていただき、近未来方向に話題を展開していただいた。
全豚の自家配運動で学んだ世代が開拓!
林 私は1974年(昭和49年)に大学を卒業して22歳で家業に入ったのですが、そのころちょうど、全豚の活動が盛んな時期で、曽我達夫さんが牽引した中心的活動の1つが自家配運動でした。アメリカ大豆協会の瀬良英介さんが講師を務め、トウモロコシと大豆粕を使ったアミノ酸レベルの配合設計を学ぶセミナーが開催されたりしましたが、生産者が200人ぐらい参加して電卓片手に、あるいは手計算で真剣に勉強していた光景を憶えています。自分の農場でも自家配に取り組みたいと思って、検討を始めたところで、赤地勝美さんを中心とした群馬自家配研究会というグループが発足して、うちの農場もそこに参加することになったのです。委託配合で、グループの仲間と共同の自家配工場をもつ形で30年以上、飼料の供給を受けました。
それが、ちょうど8年前の2011年(平成23年)に、今度は自分の経営のなかで飼料工場をつくって、本格的に自家配に取り組み始めました。何が契機になったかと言うと、10年くらい前に海外、とくにデンマークにあらためて視察に出かけてみて、当時注目された繁殖を中心とした育種改良だけでなく、現場の飼養管理技術も随分進歩していて、小規模の経営でも多くが立派な飼料工場をもって自家配に取り組んでいること、飼料の内容についてもたくさん知識をもっていることに感銘を受けたということがあります。レベルの高い農家をたくさん見るなかで、色々考えさせられたところがあって、自分の農場でも自家配をもう一度考え直す必要があるなと強く感じたわけです。
吉角 1995年(平成7年)1月17日、事務所に出ると誰もいなくて、皆、食堂でテレビに釘づけになっていました。早朝に阪神淡路大震災が起こった日でした。高速道路が分断されたところにバスがかろうじて落ちずに傾いている光景に目を奪われながら、その日の日経新聞に目を落とすと、小さな記事でしたが、飼料用丸粒トウモロコシの無税輸入が解禁になるということが報じられていたのです。皆がテレビを見上げているなかで私1人、下を向いてその記事に釘づけになったのを鮮明に憶えています。
取引先の養豚家に電話してみてもなかなか知っている人がいませんでしたが、ニュースの内容は間違いでなく、やがて全豚から熊本の生産者にも、地元で支援してもらった国会議員にお礼を伝えるようにという指示も回ってきました。実際には、その年の4月1日付けで解禁となって、全豚は6月に早速、全鶏と合同でアメリカに自家配の視察団を送って、栄養や配合設計、関連資材の情報を集めて帰り、その足で帰朝セミナーを開催しました。その視察先で、カンザス州立大学の栄養の先生から、トウモロコシの粉砕機のメーカーとして紹介されたのが、デービスという会社だったのです。
それが縁で日本の丸粒自家配農家は以来20年近く、このデービス社の粉砕機を使うことになるわけです。私もそこに深く関わることになったのですが、この粉砕機は故障も多く、皆さん大変な思いをしながらこの機械を使ってこられました。
林 吉角さんは、元々は飼料関係ではなかったですよね
二種混からの転換で不可欠となった「デービス」
吉角 はい。私は当時、動物用医薬品の卸会社に勤めていました。動物薬の営業の一環として、丸粒自家配に取り組もうとしている生産者に、粉砕機の輸入斡旋をする形で関わり始めたのです。ワクチンだ、飼料添加剤だという営業をしていて、何か場当たり的で…面白くなくなっていたところがあったかもしれません。もう少し踏み込んで養豚家の役に立つことができるのではないかと思うところもありました。
林 吉角さんが関わって最初にデービスの粉砕機を入れたのは誰でしたか?
吉角 私の地元である熊本の田中さん、田代さん、齊木さん、そして福岡の中村さん松永さんの5人が、まとめて5台買うということになり、輸入のお手伝いしたのが最初でした。田中さんや田代さんは、その前から二種混原料を使って自家配をやっていましたが、初めて自家配を始める方もいました。彼らは九州では一番乗りだったと思いますが、日本で最初に丸粒自家配に取り組んだのは、千葉県干潟の加納さんたちのグループだったと思います。いずれにしても、この1995年の丸粒解禁の直後に導入した方々が、言わば丸粒自家配の“第一世代”と言ってよいのではないかと思います。
林 だとすると、最初にお話した全豚初代会長の曽我達夫さんたちは“ゼロ世代”と言えると思います。自家配運動を展開して規制緩和、丸粒の自由化を求めて飼料栄養の知識や技術の普及に努めた。だいたい昭和50年代のころです。群馬でも大脇式の攪拌機をもって自家配を実践している農場がたくさんありました。そうした運動が20年くらい続いて、やむなく二種混で自家配を実践していた千葉の加納さんや熊本の田代さんたちが、やがて丸粒の先駆者になっていったわけですね。
吉角 田代さんたちが丸粒を使い始めて実績を上げ、口コミで宮崎や長崎で丸粒自家配が一気に広がったのが、1998年(平成10年)でした。この年を中心に、私が関わっただけでも熊本、宮崎、長崎を中心に30台くらいはデービスの粉砕機と自家配合施設を導入したと思います。
林 田代さんの影響は大きかったと思います。興味のある人には誰にでもオープンに農場も飼料施設も見せてあげて、稲吉さんが丸粒全粒粉の指定配グループ“やまびこ会”を立ち上げたのも、田代さんの農場を実際に見て決断したし、私も自家配を検討し始めたあと、田代さんの農場は見せてもらいました。
吉角 丸粒自家配をやった農場では、平均して20日ほど出荷が早くなったとか、飼料価格は配合に比べてt当たり1万円程度安くなったとか、そのダブル効果で儲かるようになったよ、という評価が多かったですね。そのうち、南九州でも結構な大手が自家配に変わっていって、飼料メーカーさんからは大いに睨まれました。最終的にはデービスの機械を100台くらいは扱いました。大型の機械も一応ありました。デービスの粉砕機はローラーミルというタイプの粉砕機で、飼料メーカーで使っているハンマーミルに比べると細かく均等に挽けるということにはなっていましたが、今から思うと、非常に稚拙なもので、よく故障して部品の交換も多くて苦労しました。
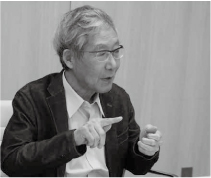
1993年(平成5年) | 12月 | ガット・ウルグアイラウンド(UR)合意 |
1994年(平成6年) | 5月 | 全豚会議など UR 対策の一環で規制緩和要求(丸粒など) |
12月 | 大蔵省関税率審議会答申で丸粒無税化の方針決まる | |
1995年(平成7年) | 1月 | 1月17日に阪神淡路大震災 |
2月 | 全豚丸粒セミナー | |
4月 | 飼料用丸粒トウモロコシの無税輸入(関割制度)解禁 | |
6月 | 全豚会議などアメリカに自家配事情等の視察団派遣 | |
6月 | アメリカ視察団の帰朝報告「丸粒活用実践セミナー」開催 | |
12月 | 千葉県・(農)干潟企業養豚が二種混から丸粒に転換 (国内養豚で最初の本格的な丸粒自家配実践例) | |
1996年(平成8年) | 2月 | 全豚丸粒セミナー |
8月 | 栃木県・曽我の屋農興(株)が二種混から丸粒転換 | |
10月 | 熊本県・(有)田代養豚が二種混から丸粒に転換 | |
1997年(平成9年) | 6月 | 丸粒全粒粉を使う指定配事業で「やまびこ会」立ち上げ (田代氏の実践例から愛知の稲吉氏ら。豚事協のモデルに) |
1998年(平成10年) | 6月 | 宮崎県で丸粒自家配の導入ブームに |
2011年(平成23年) | 1月 | 群馬県・(株)林牧場で丸粒利用の飼料工場稼働 |
メンテナンスの苦労、機械の限界
林 うちでも自家配を始めて最初の2年か3年かはデービスを使いましたが、本当によく壊れて、正直なところ、もてあましました。粒度を細かくするためのすき間の調整も難しかったし、ローラーを替えてもいきなり故障するし、ベアリングの消耗も激しかった。何より音や振動がすごかったですね。それもエネルギーを使って出しているわけだから、電力も相当無駄に使っていたと思います。日本では皆、デービスは米国の主流メーカーだと思っていたんだけれど、実はそうではなくて、主流のメーカーは別にあった。うちも、実際に機械を動かしていたのは息子たちで、相当ストレスがかかっていたはずです。それで、主流メーカーの最新の機械に替えようかと思っていたところに、ちょうどデンマークのSKIOLDというメーカーの粉砕機が紹介されたのです。
吉角 デービスも、最初に大学から紹介されたこともあって、最高の機械だと思って導入したのですが、実際使ってみると、色々問題が出てきたわけです。
林 逆に、日本の小規模の農場でも買えるような小型で安価な機械を紹介されたからこそ、最初の普及が成功したとも言えると思いますよ。確か200万円しないくらいで買えましたよね。あとから段々いい機械が出てきたということで、車でも何でも技術の進歩とはそういうものです。だから、デービスの粉砕機が日本の丸粒自家配の黎明期に果たした役割は大きかったし、その普及をサポートしてきた吉角さんの功績が霞むわけでもないと思います。
吉角 そう言っていただくとありがたいです。そして、林さんのおっしゃったSKIOLDの機械が入ってきて、林さんのところもそうですが、丸粒自家配の粉砕機が数年のうちに、デービスからSKIOLDへと一気に入れ替わってきました。このSKIOLDで自家配を始めた世代が、丸粒自家配の“第二世代”にあたると思います。二種混から丸粒に変わったことで何が変わったか、というところで、少し若い人に参考にしていただければと思うのですが…。二種混とは、トウモロコシを粉砕した単味の原料が流通すると、それが本来は無税のトウモロコシを使えないコーンスターチ業者に横流れする恐れがあることから、魚粉などのタンパク原料をあらかじめ混ぜたうえで流通されていた原料です。
その二種混は、自家配農家には500kgのトランスバック単位で入ってきて、それをクレーンで下ろしたところに、どの副原料をどれだけ混ぜるか、という作業をしていたわけです。
それが、丸粒トウモロコシを買ってくるとなると、まず、どうやって量を量るかというところから違ってきます。まず、粉砕したらタンクに入ってしまうので、ロードセル(計量器)をつけられればいいのですが、小規模のところではタイマーを使って時間で量を計るケースが多かったです。だいたいタイマーで計ると1000分の8程度の誤差で、ロードセルで計っても1000分の2くらいの誤差がでますから、それほど大きな差が出るわけでもなく、配合上は無視できる範囲でした。現に、九州の自家配農家はほとんどがタイマーで計量していましたが、それで問題が起こったケースはなく、だいたいうまくいきました。混ぜるものは、基本的にトウモロコシと大豆粕がほとんどです。それで基本的に豚は飼えるので、そんなに厳密にやる必要はありませんでした。
林 日本で、養豚農家向けに飼料製造のプラントを提供できる業者さんがいなかったので、吉角さんのように、自家配合施設の導入サポートする、その周辺のエサの配合や施設に明るい人がいたことはありがたかったと思います。
丸粒使用で注目された粉砕の“粒度”
林 二種混の時代に、当時は4つ割りとか8つ割りと呼ばれて、3mmも4mmもあるような粒度のトウモロコシでしたが、それが形を残してふんに出てくるものだから、アメリカから栄養の先生が来たときに生産者が、「これは十分消化されていませんよね?」と質問する場面が何度かありました。ところが当時のアメリカの大学の先生は、「形は残っていても、栄養成分はきちんと消化されて吸収されている」と答えるのが常でした。おそらく、粒度と消化率ということが彼らのなかでも、まだあまり意識されていなかったのだと思います。ただし、「細かくしすぎると胃潰瘍になるから注意しろ」、ということは言っていました。まだ機械の性能的に細かく挽けなかったこともあっただろうし、自分の農場で育てた安いトウモロコシがいくらでも使える環境だったと思いますから、その辺の研究も進んでいなかったのかもしれません。しかし、丸粒トウモロコシが解禁となったころになると、カンザス州立大学でも粒度を細かくすると消化率が上がるという研究結果も出ていて、全豚の技術顧問だった福田正夫先生が訳して冊子にして全豚で配布していました。ですから、丸粒自家配に取り組んだ生産者は皆、粉砕粒度には関心をもって取り組んでいたはずですが、デービスの機械を使っている間は、ままならなかったのが現実です。
自家配の体験でこそ磨かれる経営者マインド
吉角 林さんが自分で工場をもって本格的に自家配を始めたのは2011年ということですから、丸粒が解禁になってから15〜16年も経ったあとですね。色々考えることがあったということでしたが、もう少し詳しく方針転換の理由を教えていただけませんか。
林 自家配研究会と名前はついていますが、委託配合だと配合飼料を買っているのと同じで、栄養の勉強会とかはやっていましたが、原料を仕入れてもらって、配合設計もしてもらって、混ぜて運んでもらうということを長く続けているうちに、依存体質になってしまっていたんですね。自分でリスクも負わないから、経営の経験としての蓄積にもならない。それではまずいな、と思った。そこに気づかせてくれたのが、最初にもお話したように、デンマークの養豚だったのです。彼らは自分たちの豚に食べさせるえさのことを我々よりずっと真剣に考えています。我々も通り一遍のことは分かっていますが、そういう知識が現場とつながっていない。そういうことを痛感したわけです。私自身、実際に8年間、自家配をやっていきてはっきり言えるのですが、実はそこの部分というのは経営者にとってすごく大きなポイントなのです。自家配を実践するということは、飼料原料を1つひとつ自分で買ってこなければならない。配合飼料を買っていると、トータルの価格のなかで、トウモロコシの価格はこうだから、為替の動向がこうだからということはメーカーから説明されるけれども、個々の原料の価格は分からないで済まされます。しかし、その価格動向や背景を知るか知らないか、知りたいか知らないで済ませられるか、そこは感性の問題だと思うのだけれども、今は母豚100頭の一貫経営だとしても、20年後には2000頭の経営になっているかもしれない。その将来を決めるのに、その感性の差が大きく影響してくると思うのです。それは経営者の姿勢だとか思想に関わることだと思います。
吉角 林さんところは規模が大きいから自分で工場をもって人手をかけても採算が合うと皆さん思っていると思いますが、そうではなかったのですね。ただ、中小の規模だと、設備投資して、人員を配置し、加工賃もかけてとなると、自家配はかえって飼料コストを上げるという指摘もあります。
林 コストとなると、それまで使っていたえさとの価格差もあるし、それぞれの経営の事情や経営者の考え方に左右されると思いますが、私が言っているのはもっと大きなところの経営メリットなんです。規模拡大することで、えさをつくるコストが薄まるというレベルの話ではありません。
まず、自家配をやると、えさを買うサイトがなくなります。3ヶ月、4ヶ月を飼料メーカーにみてもらっていたのが、自家配を始めると、買った翌月の末にはきちんと代金を支払わなくてはならなくなります。それだけのことですが、そこでまず自然と“健全経営”の方向に向かうことになります。そして、自分で原料を調達してえさをつくって与えた成功体験が、次のステップへと向かわせてくれる。実際、自家配を始めた生産者の多くが、そこを起点に規模拡大しています。私自身も、自家配を始めたあと、その前の母豚5000頭規模から数年のうちに一気に倍以上に拡大しています。養豚家としての自信につながっていきました。
吉角 林さんの成功体験は、かつての田代さんたちの成功体験と同じように、若い人の心を惹きつけたと思います。
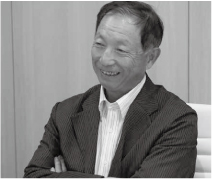
最初は先物取引で原料を買って“現受け”で入手
林 私にとってもう1つ大きなきっかけとなったのは、吉角さんが提唱していた「現受け」という買い方に興味をもったことです。当時は東京穀物商品取引所で相場が立っていて、そこで先物を売買しながら最後は現物で受け取るという方法です。1つの売買単位が「1枚=50t」で、当日の新聞相場を見ながら、「何月限を何枚買って」ということで業者に頼んで買いを入れます。ところが、1枚50tとなると、うちだと月に4000tくらい買っていましたから問題ないのですが、小規模の農場ではなかなか大変な量になるので、誰も利用しなかった。それで、私が初めて使ったのです。商品取引所は先物を取引するための市場だから、通常は売ったら買う、買ったら売るで、相場の売買で利益を得ようとする人が参加することで成り立っているのですが、養豚家は豚のえさを調達することが目的だから、豚を売って採算がとれる範囲で、ある程度納得できる価格でトウモロコシを買えたら、最後はトウモロコシを現物で受け取ることで決済できるわけです。ただし、東京穀物商品取引所で買ったトウモロコシの現物が、どこから出てくるかわ分からない。だけど、私の農場は群馬にありますから、鹿島でも千葉港でも横浜でも、それほど輸送距離は変わらず引き取ることができます。そういうことで始まったわけです。その方法でトウモロコシを調達すると、かなり原料コストを抑えられるという見通しが立って、それも、私が自家配に向かう大きな動機になりました。
吉角 トウモロコシの先物取引が始まったのと、丸粒トウモロコシの関割制度が始まったのが同時でした。丸粒トウモロコシを買う農家は、商品取引所を利用して調達しなさいよ、というのが農水省の推奨だったのですが、実際にはほとんど使われなかった。ただ、よく勘違いされるのは、東京穀物商品取引所の相場、そのままの価格で買えるかというと、そうではないんです。
林 それはウソというわけではなくて、指し値で買えた価格に対して、t当たり数千円の商社の手数料が加算されるわけです。サイロ渡しだと、自分で引取りに行けば、かかるお金はそれだけです。それでも、実際かなり安く買えました。そういう形の取引を、自家配を始めた2011年のはじめから5年くらい続けたでしょうか。
吉角 今はどうしているのですか?
林 今は、先物取引で買った価格に商社の手数料を乗せた金額よりも、直接、商社から買うほうが安く買えるようになっていて、商社から買っています。先物取引でも、1枚:50tの単位だと買える人がいなくて、1日に1枚とか2枚という取引で、相場が形成されなくなった。トウモロコシの先物取引は2013年に東京工業品取引所に移管され、東京穀物商品取引所は解散してしまいました。先物で手当していた数年間は、朝5時からテレビでマーケット情報番組を視ていました。それは今でも視ているのですが、当時はさらに、しっかりメモを取りながら視ていました。ここが買いだと思って買っても、さらに一段二段下がって“損”をしたと思ったこともありましたが、さっきもお話ししたように、自分は豚のえさを買うことが目的で、豚を飼って儲けることが仕事だという原点に立ち戻れば、日々の相場で切った張ったするのは自分の仕事じゃありません。ただし、楽しい経験で、勉強にもなりました。
粉砕機はローラーミルからディスクミルに
林 私の農場で自家配工場を立ち上げたのが2011年(平成23年)の1月で、竣工当初はデービスの粉砕機を導入しました。色々試行錯誤はありましたが、粉砕機のトラブルが多いのも大きな問題で、アメリカの、デービスよりも主流のメーカーからの導入を検討しているところに、吉角さんからSKIOLDというメーカーがあるということを聞いて、検討した結果、粉砕機を取り替えることになりました。それで正解でした。SKIOLDの粉砕機は「ディスクミル」というタイプで、デービスの「ローラーミル」とは根本的に構造が違います。粒度も自由自在に調整できるし、音も静かで振動も少ない、ホコリも少ないし、故障はほとんどないと言っていいくらいありません。要するに、とんでもない差があったわけです。
吉角 SKIOLDは、今から10年以上前にデンマークの砂川さんから「こんなものあるよ」と言うことで紹介されたのが最初でした。長崎のお客さんが早速興味をもたれて「使いたい」ということになりました。それで入れたところが、いきなり故障したのです。それも「ボカーン」とケースごと割れてしまった。「何だこれは!?」と調べてみると、どうも石か金属か、何か硬いものがトウモロコシに混じっていて、それを挽いて壊れてしまったようなのです。それで、メーカーにクレームすると、「デンマークの小麦にはそんな石やらボルトやらが混じることはないから対応していない」と言うのです。
最終的には、粉砕機にかける前の段階でふるいを通すことによって使えるようにはなるのですが、そのときは、トラブルがあったために、しばらく次の導入は控えることになってしまいました。
林 ふるいは必須ですね。デービスの機械にも、大雑把なものですが、ふるいはついていました。デンマークの小麦と比較してどうかは知りませんが、アメリカのトウモロコシを使う限り、夾雑物の対応は不可欠です。ローラーミルは少しくらい大きな夾雑物は受け入れるだけは受け入れますが、ローラは傷みますから、ますます細かくは挽けなくなっていきます。ディスクミルの場合は構造上、夾雑物、異物を受けつけませんよね。
吉角 そうなんです。先ほど紹介した長崎の導入の失敗例のあと、しばらくして導入したいという人が出てきて入れたところ、また同じように壊れてしまった。やはり原因はボルトか何かが混ざっていたことだったのですが、メーカーは一向に対応してくれなくて、仕方なくて自分で対応することにしました。
林 それで、吉角さんが「トロンメル」を開発したわけですね。要するにSKIOLD用の回転ふるいを開発したことで、一気に安定して日本でも使えるようになった
吉角 元々「トロンメル」と呼ばれる回転ふるいは工業分野で使われていたもので、それを応用したものですが、これで結構細かい異物まで取り除けるようになりました。メーカーはディスクの寿命について、先ほどの20馬力の機械であれば、1万t挽いたら交換を推奨していたのですが、実際に1万t挽いたところで開いてみると、全くディスクが摩耗していなくて、しっかり挽けるわけです。それで、まだ使えるということで2万t挽いたところで見てみると、まだ減っていない。そうこうして、5万t挽いたところで、いくら何でも交換しようということで、まだしっかり挽けてはいたのですが替えてみました。そのあと、砂川さんがSKIOLDの担当者をデンマークから連れてきたときに、「1万tと書いてあるのに、どうしてパナマックス1隻分も挽けるのか?」と聞いたところ、色々調べたうえで、トロンメルをつけたことで、大きな異物だけでなく、砂や砂鉄など細かい異物も除去できていて、それでディスクの傷みが少ないんだということになった。今ではSKIOLDもトロンメルを作って一緒に売っています。 同じ20馬力のデービス粉砕機とSKIOLDの粉砕機を比べてみると、デービスが1時間に2t粉砕するのに対し、SKIOLDは5t挽けます。同じ馬力のモーターでそれだけ性能の差があるわけです。それで、細かく均一に挽けます。
林 うちの宮崎の農場で導入した粉砕機も、既に4万t挽いていますが、まだまだ使える状態です。
吉角 粉砕機の歯を摩耗させているのはトウモロコシではなく、砂や砂鉄だということです。
裕一朗 少し私のほうから補足させていただきます。トロンメルというのは、少し斜めに傾けたドラム状の2重のふるいを回転させたなかに、原料トウモロコシを投入すると、最初に大きな目の1枚目のふるいでトウモロコシは下に落ちて、それより大きな異物や夾雑物が取り除かれます。さらに斜めにドラムを移動するなかで、今度は2枚目のふるいで、トウモロコシより小さい異物がふるい落とされて、トウモロコシだけが残って、粉砕機に投入されるという仕組みです。細かい「粉」も相当量出ますので、それはまたかき集めて、オーガーで粉砕機の先、混合器に投入できるようになっています。
斜めに設置するドラムの角度と、ふるいにかかる長さ、2つのふるいの目の大きさの調整がなかなか難しかったですが、改良を繰り返しながら、なるべくコンパクトな形で完成したのが今の製品となっています。
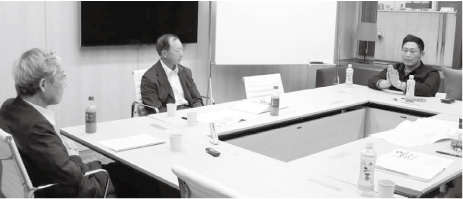
吉角 日本がアメリカから買う飼料用トウモロコシは、USDAの格付等級のNo.3のものですが、実際にはNo.2とNo.4を混ぜ合わせてつくっています。いわゆる夾雑物(BCFM:破損穀粒と異物)は4%以下とされていますが、これは結構な割合です。
林 ですから、先ほども言いましたが、穀物原料を使うときに夾雑物の混入は前提として考えておかなければなりません。ボルトやネジなどもざらに入っています。
飼料危機を経て丸粒自家配も次のステージに
林 過去10年を振り返ってみると、2008年から2009年にかけて世界的な穀物の不作で、米国産トウモロコシも高騰して1ブッシェル8ドルまで上がりました。そこへさらにリーマンショックで投機筋の資金が商品市場に入ってくるようになって、シカゴ相場はその後も高止まりを続けて、飼料費が上がってしまったという状況がありました。石油の代替燃料としてエタノールの需要が伸びるなかで、先行きの先高感もあって、何とか飼料費を抑えたいと誰もが考えていた時期であったということが大きかったと思いますね。
トウモロコシの価格が上がって大変なのはアメリカの畜産だって同じだから、アメリカの養豚産業も、飼料原料が高いなかでいかに飼料費を抑えるか、要するに飼料要求率をいかに改善するかが業界全体の重要課題になっていた。そのなかで、トウモロコシの粉砕粒度を細かくして消化率を上げようということもあらためて研究テーマになったのだと思います。
粒度の問題は、細かすぎると胃潰瘍になることは間違いないけれども、20年前には0.7mm程度がいいという話になっていましたが、最近では研究も進んで、アメリカでは0.4mmくらいが推奨されていますね。ただし、胃潰瘍が発生する粒度とのバランスがある。そうした情報が日本にも紹介されるなかで、あらためて自家配が注目を集めるようになり、簡単に粉砕粒度を調節できる「ディスクミル」タイプの粉砕機が盛んに導入されることになったのだと思います。
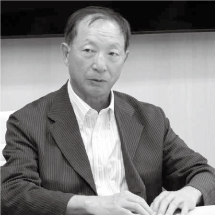
吉角 丸粒トウモロコシの自家配が始まった1995年以降の20年近く、自家配では必ずデービスが使われてきて、それが急激にSKIOLDに置き換わり始めたのが確かにリーマンショックのあと、2010年ころでした。新規の自家配実践者はSKIOLDを入れましたし、従来のお客さんも急激にSKIOLDに変わっていきました。
林 飼料高騰も絡んで、飼料用米の利用が推奨されて、完配利用の農場が部分的に飼料用米を使う場合でも、玄米なり白米を粉砕しなければならないという事情も出てきたころでしたね。
吉角 そうです。ディスクミルだと、籾のままでもきれいに挽けますから、米どころの畜産農家からの引き合いが多くなりました。玄米で買うとなると加工賃を取られてkg当たり40円、50円にもなりました。あるお客さんが「籾で飼料用米、買い取ります」とチラシを新聞に投げ込んだら、ひっきりなしに電話がかかったという話もありました。
林 籾だと、消化率は少し落ちますね。
吉角 はい。2割くらい落ちます。
林 ただ、繊維分は母豚にとっては必要で、繊維原料を混ぜようと思うと、かえってトウモロコシよりも2〜3倍も高いですから、使いようだと思います。最近では、肉豚飼料への利用性も指摘されていて、粉砕粒度の問題と絡む胃潰瘍の抑制効果があるという研究成果もあるようで、少し関心をもっています。ただ、繊維と言っても様々なタイプ、製品も出てきていますので、その辺は、十分検討する必要があります。
吉角 そこがなかなか難しいようで、今は、籾から粉砕して使っているところは少なくなって、飼料用米は玄米で買っているとことが多くなっています。
林さんも、そのころにSKIOLDに変更されましたが、粉砕粒度は今、どのくらいに設定していますか?
林 うちは豚の状態を見ながら、0.4mmのときもあれば、胃潰瘍が出たりしたら0.7mmくらいで挽くこともあります。そこは現場の様子を見ながら時々調整しています。
ただ、現実には、ほかの条件が理想的であれば、0.1mm単位の調整で差が出てくるのかもしれないですが、実際には様々の要素があって、粒度以外の問題も必ず何かあるのが現場ですから、そう厳密にコントロールすることもできないし、その必要もないわけです。ですから、理屈は理解しておくべきですが、あまり神経質にならないほうがいいでしょう。
飼料用米の利活用も自家配の追い風に
吉角 飼料原料の高騰と、減反政策の見直しに絡む形で、政府は飼料用米への作付転換を推奨するようになりましたが、林さんのところでは、飼料用米やMA米は使っていませんか?
林 うちでは使ったことがないです。かなり飼料用米が安く出回ったこともあって、原料用タンクを増設して使ってみようと考えた時期もあったのですが、最近はあまり、飼料用米が安いという話を聞かなくなりましたので、使うことがないまま、ずっとトウモロコシを使っています。
裕一朗 熊本県でも、八代の稲作農家の方が一時、飼料用米をかなり作付したのですが、いざつくってみると、使ってくれる畜産農家が見つからないというミスマッチがありました。飼料用米に一度転作すると、食用米に戻すのに非常に手間がかかるそうで、飼料用米は作付されなくなったという事情もありました。地域のなかで、飼料用米をつくったらしっかり飼料に使ってくれる一定規模の畜産農家があるのかどうか、そういうニーズを把握する情報の交流が不可欠だと思います。そこのところのマッチングを農協などが主体になってうまくできているところも確かにあるのですが、熊本はうまくできていないということだと思います。地域によって取り組みに大きな差があります。
林 これまでは政府が相当の補助金をつぎ込んで飼料用米への転作を奨励してきたけれども、将来的にどこまでそれが続くか、不透明だと設備投資できない、積極的には使えない、という事情もあると思います。
それと私の場合、飼料はなるべく単純系にしておきたいという気もちがあります。例えば、飼料原料や配合設計で飼料要求率を改善できる余地はあるのだけれども、どこまで費用対効果が得られるかという問題なわけです。さっきもお話ししたとおり、えさ以外の要素に左右される部分が大きいなかで、栄養の細かい操作の成果をどこまで評価できるのか、その再現性があるのかどうか、そこは難しいですよね。我々はあくまで養豚家であって飼料メーカーではないから、自分でつくった飼料を豚に食わせていくらというところが本業なので、そこをベースにした判断でいけばいいということだと思うのです。飼料の栄養の精度を上げようとすると、そこに人手もコストも必要になります。だから、人工乳は自分でつくるのはやめて、そこは飼料メーカーから購入しているわけです。
私自身、マニアックに自家配したいとは思っていないので、100点満点のえさをつくろうとは最初から考えていなくて、「80点とれたら十分だ」くらいに考えています。実はそのところは“経営”としては大事なところではないかと思っています。
数年前のPED、そして今回の豚コレラ問題を踏まえて、これからは飼料も含めて防疫・衛生へのリスク管理の対応が益々大きな要素になってくると思います。そうなると、経費面の課題も考えていかなければならなくなるでしょうね。
自家配養豚のための栄養学とテクノロジー
林 ところで、吉角さんがコーンテックで独立されたのはいつでしたか?
吉角 2010年です。その前から体調を崩したこともあって、会社には辞めたいとは希望を出していたのですが、古くからおつき合いの続いていたお客さんもいましたので、会社に出てこなくてもいいから籍は置いておいてくれと請われて、定年後も2年間務めました。会社を辞める前後のころ、林さんが話された飼料高騰という時期でもあって?、それまで自家配は九州のお客さんがほとんどだったのが、関東や東北、北海道からも声がかかって出かけていくようになりました。自家配をやりたいと思ったときに、アドバイスできる人が地元には誰もいないということでした。なかなか情報がありませんでした。
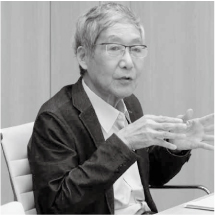
林 アメリカでは昔、自家配農家向けに、トウモロコシと大豆ミールがあれば、あとはこれだけ加えればいいという自家配用サプリメントが結構出ていましたが、日本では、そこまでのサプリメントは流通しなかったと思います。だから、自家配をやると、ある程度の配合の知識はもったうえで、主原料副原料をほとんど自分で調達してきました。そうやって自分で調達した原料でえさをつくって与えていると、豚で何か事故が起こったときに、えさの原因は除外して考えられます。それは経営者としての自信にもつながる。
吉角 初めて自家配に取り組む方は、栄養の知識を十分にもっていない方もおられるので、求められば、私のほうで配合設計して、「これで混ぜてください」という情報提供もしています。私どもで過去20年以上、丸粒トウモロコシの自家配をお手伝いしてきたところで、それで失敗した人はいません。
裕一朗 古谷修先生が畜産試験場の熊本にある九州支場におられたときに、父が地元の縁で交流する機会があって、『日本飼養標準・豚』、『日本標準飼料成分表』のデータベースと、古谷先生の手持ちのデータなども提供いただきながら、最初はポケコンで、自分でプログラムを組んで打ち込みながら、1つの計算をするのに1時間もかかりながら配合設計をしていたそうです。その後、パソコンが普及してWindowsが出て、エクセルが使えるようになると、エクセルのソルバーという機能を使ってアミノ酸スコアまで瞬時に計算できるようになって、我々としては、自家配に挑戦する生産者にハードとソフトを合わせて提供できる態勢ができていったということです。古谷先生との出会いがなくて、粉砕機だけ売っていたとしたら、ここまで続いていなかったと思います。
林 私も、吉角さんの設計も見せてもらって参考にしましたし、米国NRCの飼養標準や種豚メーカーのマニュアルなども勉強して、それらを見ながら、「このくらいでいいのかな」という数字を決めて配合しました。ただ、最初のころからすると、色々試行錯誤もしながら、配合内容は随分変わってきています。古谷先生の書いた『飼料を極める』からも、大変勉強させていただきました。
試行錯誤として1つあげると、一番最初のころ、離乳期のえさを、NRC飼養標準を参考にしてつくったのですが、それで下痢が続いて苦労しました。アメリカの配合は、離乳期でもタンパク質のほとんどを大豆ミールで供給するという考え方ですから、大豆ミールの配合割合が30%以上にもなるんです。そのことが問題を引き起こすという知識がなかったものだから、NRCを鵜呑みにしてやったわけです。ともかく下痢に悩んで、大豆ミールの配合割合を徐々に下げていき、必要なアミノ酸は単体アミノ酸で補っていくようにして、ようやく安定しました。アメリカでは、NRCだけでなく、アイオワ州立大学やカンザス州立大学でも、似たような配合設計を推奨して、おそらく大きな問題は出ていないのが不思議なところです。えさだけではありませんが、アメリカでうまくいっていることが、そのまま日本でもうまくいくとは限らないということを学ばせてもらいました。それ以外には、大きな失敗はありませんでした。
裕一朗 自家配を実践しようとすると、まともに考えると対応する要素が非常に多くあります。それらを1つひとつ対応し、テストしていくには経営者1人、担当者1人の限界を超えています。
林 それはあるね。
裕一朗 そのなかで最終的に、これまでは経営者の勘に頼ってやってきたわけです。
ところが最近では、野球でもバスケットボールでも将棋でも、競技そのものには全くの素人がデータサイエンティストとして、データを徹底的に解析していくことで、相手の弱点とかゲームの戦略・戦術とかをビッグデータから出てくる数字を頼りにして圧倒的な成果をあげています。そうした人たちのことをゲームチェンジャーと呼んでいますが、広い意味での異業種参入ですね。
それからすると、畜産分野でも、日常管理のなかでのデータやベンチマーキングのデータを、コンピュータがA(I人工知能)を使って、相当に感度の高い判断ができてくるのです。例えば、車を運転したいと思ったときに、エンジンのこととか、キャブレターがどうだとか、今の人はほとんど勉強しないじゃないですか。それでもハンドルを握ってアクセルを踏めば運転できる。そこまでもっていくというところが、テクノロジーにできる部分だと思うのです。「勉強します」とか「頑張ってます」とか、漠然とした感情論ではなくて、“これを使えば、間違いなく結果が出る”というツールを提供していくことがテクノロジーの力です。それこそが、私たちコーンテックが今取り組んでいる分野です。
林 飼料栄養のことだけ考えると、理論値も決まっているし、どの原料を使うかは価格で決まってくるけれども、それを食べる豚の状態に左右される部分も小さくないから、なかなか難しい面もあるよね?
裕一朗 そうなんです。例えば病気にかかっていたりして、健康状態が悪いとか、温度が高かったり低かったりとか、栄養の要求量に大きな影響を及ぼします。しかし、そこでもやはりテクノロジーの使える可能性が高まってきています。温度や湿度は、従来からあるセンサーを使ってモニタリングできますが、例えば豚の体温でも、赤外線カメラでモニタリングすることができるし、豚の活動レベルも画像解析で把握できます。飼料の食下量、飲水量も常時モニターできる技術が既に身近なものになってきています。それらをネットワークで結んで人工知能(AI)で分析したうえで、温度設定、給餌量、体重、さらには栄養設計なども修正していくことができれば、今よりずっと高い精度で、かなりの操作を自動化できます。
私は父とは別に、2007年から再生バッテリーを、インターネットを通じて販売する事業をしています。IT畑で違うジャンルではありますが、コーンテックの事業にも関わってきています。バッテリーの事業は、すべてデジタルで正確なデータ管理ができて、それを元にかなり精度の高いシミュレーションができるのですが、養豚の場合は、“生きた豚”という複雑系をどうしても通らなければなりません。そうなると、経験とか、知識とか、特別な計算をする能力がなければ答えが出せないわけです。それは、私のようにアウトサイダー的な立場からこの業界に入ってきた人間にとってはハンディにもなりますし、養豚場で働いている、働こうとしている人たちにとっても同じことが言えると思うのです。人の勘に頼っていた部分を何とかクリアーにしたいと思っています。人は、見えないものは怖いし、真っ暗ななかで前に進むことは困難です。そこを数値化して見えるようにしていく必要があります。
ですから、自家配に取り組もうと思うと、一般的には、まず栄養の勉強をして、原料事情を把握して、配合設計はどう計算する…、というところから始めることになります。これは、自動車を運転するときに、エンジンの構造から勉強し始めるのと同じです。でも今の世のなか、そんなことをする人はいなくて、教習所で教えてもらうのは運転の技術です。
父は父で業界に貢献してきたので、その路線は維持し、私の新しい考え方を採り入れて、これまでと違ったアプローチで、さらに大きな業界貢献ができたらいいなと考えています。それが、新生コーンテックの目指すところです。
林 お父さんもそういうところがあると思うけれども、裕一朗さんは、養豚という世界のなかでものを見ていないで、どちらかというと工業の世界と言うか、外からこの業界を見ていて、そうだからこそ、この業界のうまみも課題もよく見えているところがあると思います。発想が全然違うところがある。先物取引の「現受け」の話もそうだし、ときどき情報発信されているなかでは、陸上の輸送と海上輸送のコストの違いで、船の重量当たりの馬力は非常に小さいとか、飛行機で貨物を運ぶ燃費を考えるときに用いる「ペイロード」という言葉の解説とか、とても勉強になります。
船を大きくした場合、船の容積は長さの3乗で増えるのに対し、船の表面積は2乗でしか増えません。船の受ける抵抗は主に表面積に比例しますから、当然、海水の抵抗もおよそ2乗の関係となります。これを「2乗3乗の法則」と言います。抵抗の増加に伴って燃料消費量が増えますが、貨物の積載量がそれ以上の割合で増えるため、貨物重量当たりの燃料効率は大きく向上するわけです。
日本の飼料コンビナートがある港では、これまで1ヶ所も“ニューパナマックス”を接岸できる港がなかったのですが、北海道の苫小牧港が、突堤をずっと沖まで伸ばして接岸できるよう工事が進んでいます。こうした港湾整備が進むと、飼料の海上輸送コストが下げられると思いますね。
林 北海道の酪農や肉牛生産がすごく良くなっていきますよ。そこは注目しています。
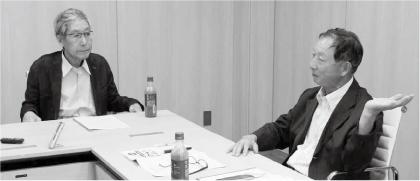
地球規模の視野で考える飼料・畜産
林 常々言っていることですが、日本は養豚を行ううえで非常に有利な立地です。「土地も高いし資材も高いだろう!」と言われると思いますが、それ以上に、世界で一番豚肉を高く買ってくれる消費者に一番近いところで豚を飼えていることが大きいわけです。それが今、中国やベトナムなどアジアの養豚大国でアフリア豚コレラ(ASF)が猛威をふるって、中国など4割も生産力が落ちている状況があるわけです。ところが、業界のなかにいると、ASFの侵入への警戒が先に立つし、国内で豚コレラが問題になっていることもあって、世界的な潮流のなかで生じている大きなチャンスが見えない。
もちろん、この豚コレラでは私も少なからず気もちが萎縮しましたが、これらの病気さえ入れなければ、しばらくは少なくとも相場に右往左往させられる状況ではないので、大きく成長できるチャンスでもあるわけです。萎縮しているだけでなく、そういう観点で将来を考える必要がある。中国では、生産力が落ちた分、豚価が急騰しているなかで、防疫対応がしっかりできる企業的経営では相当の勢いで増頭も始まっていて、そうしたなかからは、とんでもない養豚企業がのし上がってくることにもなると思います。だから、ピンチと思えばピンチだけれど、チャンスと思えばチャンスでもあるということです。
裕一朗 情報さえあれば前向きに対応できるところ、それにアクセスできないで止まっている人がとても多いと思います。ある意味、情報コントロールされているところもあって、がんじがらめになっている人もいます。そこは、情報の平等と言うか、機会の均等を図っていくことも、これから産業全体が発展していくうえでは大きな課題だと思います。“知らない”と話が始まらないし、暗闇のなかで歩き始めることもできません。情報を得ることも経営力の1つだという考え方もあるとは思いますが、産業全体のレベルアップを目指す以上は、基本的な情報や知識のレベルは同じにしたところから競争を始めるという考え方も必要ではないでしょうか?
そういう基礎的な部分の見える化を図りながら、地ならしをしていくことがまず必要だと思っています。
林 もっともっと多くの人にベンチマークに参加してほしいですね。規模の大小にかかわらず、経営の良否にかかわらず、参加する意思さえあれば、ほかの業界では考えられないほど、お互いの経営をオープンにして、様々な情報を共有できます。様々なグループはありますが、どこで、どのくらいの規模の人が、いくらくらいでえさを買って、どのくらいの成績をあげているか、ベンチマーキングをしていくことで、単に生産成績だけではなくて、その成績をあげるためにどのくらいの人が働いて、どの程度の飼養面積を要したかというところまで追跡していくことが重要です。それがないと独りよがりになるので、そういうベンチマーキンググループに身を置いて、自分の立ち位置を理解して方向性を判断していくことが大事だと思います。
裕一朗 世界に目を向けたとき、「培養肉」とか「人工肉」なども話題になっていますが、人口がまだまだ増えていくなかで、食料問題はさらに深刻になります。日本のように、動物性タンパク質を、豚肉なり鶏肉、豚肉、魚から好きなように安定的に摂れる国は実は少なくて、世界で8億人の人たちが飢餓状態だとされているわけです。日本だって、150年前の江戸時代、庶民は十分なタンパク質を摂ることができず、平均身長が150cmくらいしかなく、有史以来一番低い時代だったと言われています。畜産は、本来は人の食べる穀物の余剰をタンパク質や脂肪に転換してストックする産業だったわけですが、グローバル化が進むなかで、一方では飢える人がいるのに、日本では大量の穀物を外国から買って畜産物を生産し、そのうえで大量の食べ残しまで出しているという現実が、誰の目にも見えるようになってきています。
そうしたなかで、今世紀後半には100億人に達する人類に、どれだけタンパク質を安定的に供給するかということは非常に重要な課題で、そのときに、家畜の飼料となる穀物を耕作する農地は限られているわけですから、より効率的につくった穀物を、より効率的に無駄なく、肉や卵に転換する必要があります。人間のフードロスを家畜に給与して肉や卵をつくり、その過程で出てくる排せつ物を肥料として穀物を生産するというサイクルが、それぞれの地域で本来の形でうまく回ることを真剣に考えなければならない時代になっていることも、しっかり認識しなければなりません。
林 大事なのは、やはり経営者マインド、志だと思います。豚コレラの問題もあって、業界全体として今ひとつ元気がないように感じるけれど、是非、前に向いていきたいよね。これから農業の時代になると言われて久しいけれど、例えば今の豚価、もう6年続いていて、私も含めて「いつまで続く?」、「もう終わるだろう」と思ってきたけれども、ひょっとしたらダテにいいのではなくて、構造的に、それだけの価値があるのかもしれない。そこを確信できれば、さらに前向きに取り組めると思うのです。立場は違いますが、同じ業界のなかで頑張っていきましょう。
裕一朗 ありがとうございます。
吉角 今日は本当にありがとうございました。
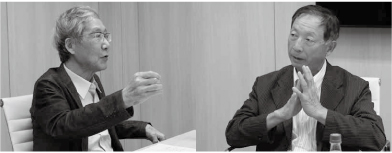
※本シリーズは、(株)コーンテックの協賛により掲載いたします。